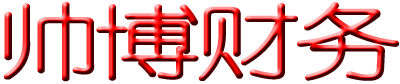
- 价格透明
- 信息保密
- 进度掌控
- 售后无忧
杩欐槸涓€涓叧浜庣埍鍥姐€佸鏂椼€佽拷姊︾殑鏁呬簨銆�
銆€銆€鍐呭湴姹夋棌骞查儴鍚撮洦鍒濓紝涓ゆ杩涙彺锛屼竴娆�16骞达紝涓€娆�8骞淬€�
銆€銆€绗竴娆¤繘锛屽惔闆ㄥ垵22宀併€傚惔闆ㄥ垵璇达細鈥滄垜鏈夊垢閬囧埌閭d箞澶氬杽鑹殑鏃忓悓鑳烇紝鐣欎笅鍒婚閾績鐨勮蹇嗭紝褰卞搷浜嗘垜鐨勪竴鐢熴€傗€�
銆€銆€绗簩娆¤繘锛屽惔闆ㄥ垵57宀併€備粬杈炴帀鍖椾含鍑虹増闆嗗洟濮斾功璁般€佽懀浜嬮暱鑱屽姟锛屽洖鍒伴洩鍩熼珮鍘燂紝浠庨浂寮€濮嬶紝寤鸿捣鈥滃~琛ュ浗鍐呯┖鐧解€濈殑鐗︾墰鍗氱墿棣嗐€�
銆€銆€鈥滄啫鍘氥€佸繝鍕囥€佹偛鎮€佸敖鈥濓紝鏄惔闆ㄥ垵瀵圭墻鐗涚簿鐨勬鎷€�
銆€銆€浜氭牸鍗氾紝鏄棌鍚岃優瀵瑰惔闆ㄥ垵鐨勭О鍛尖€斺€旇鎰忔€濇槸鈥滆€佺墻鐗涒€濄€�
鈥滄眽涓€瀹朵翰鈥濓細浠栨湁鏃忓濡堬紝涔熸湁鏃忓コ鍎�
杩涘叆12鏈堬紝鎷夎惃鐨勫厜涔熸尅涓嶄綇瀵掓剰锛岃タ鐗︾墰鍗氱墿棣嗗伐浣滀汉鍛樻鐑伀鏈濆ぉ鍦版妸棣嗗寘瑁呯銆�
銆€銆€鐜板湪鏄タ鏃呮父娣″锛�800浣欎欢鍝佸皢闅�50涓湪绠憋紝鈥滃啲椹烩€�4000澶氬叕閲屽鐨勬禉姹熺渷鑷劧鍗氱墿棣嗭紝璁╂睙鍗楄浼楅浂璺濈浜嗚В鐗︾墰鍜屾棌浜烘皯鐨勬晠浜嬨€�
銆€銆€2016骞磋繘浜煄銆�2017骞磋蛋缇婂煄銆�2018骞翠笅閲戦櫟锛岀墻鐗涘崥鐗╅寤烘垚鍚庯紝鍚撮洦鍒濆甫鐫€棣嗗湪鍏ㄥ浗澶氬湴宸″睍銆傝繖娆″埌娴欐睙宸″睍锛屾槸绗洓绔欍€�
銆€銆€鏁寸悊銆佺爺绌躲€佹挱銆佸紭鎵棌浜烘皯鐨勭墻鐗涙枃鍖栵紝鍚撮洦鍒濈殑姊︼紝缁堜簬鍦嗕簡銆�
銆€銆€2011骞达紝鏃朵换鍖椾含鍑虹増闆嗗洟鍏徃濮斾功璁般€佽懀浜嬮暱鐨勨€滆€佹彺鈥濆惔闆ㄥ垵锛屽悜缁勭粐鎻愬嚭杈炶亴锛岀敵璇烽噸杩旇タ鍦嗕竴涓ⅵ銆傜煡閬撲粬涓嶆槸蹇冩潵娼紝鐭ラ亾浠栧闆煙楂樺師鐗垫ⅵ钀︼紝缁勭粐缁堝悓鎰忎簡浠栫殑鐢宠銆�
銆€銆€57宀侀噸杩旇タ锛屼笌1976骞�22宀佸ぇ瀛︽椂鐬掔潃鐖舵瘝鎶ュ悕鎻达紝鏃㈢浉鍚屽張涓嶅悓銆�
銆€銆€鐩稿悓鐨勬槸锛岀鍥借タ閮ㄩ偅鐗囬珮鍘熷彫鍞や粬鈥滀汉寰€楂樺璧扳€濄€備笉鍚岀殑鏄紝35骞村墠锛屼粬鍒濈敓鐗涚妸涓嶁€滄亹楂樷€濓紝鎯宠荡闆煙闈掓槬鐑紱35骞村悗锛屽勾杩戣姳鐢茬殑浠栵紝鏀惧純鐨勬槸瀹夌ǔ鑸掗€傦紝閫夋嫨鐨勬槸鑹伴毦鑾祴銆�
銆€銆€浠栬骞茬殑鏄枃鍖栨彺鈥斺€斿缓璁句竴搴х墻鐗涘崥鐗╅銆傛鍓嶏紝浠栦粠娌″仛杩囧崥鐗╅宸ヤ綔锛岃緸鍘婚瀵艰亴鍔″悗锛屾墜涓嬫棤浜烘棤閽辨棤鍝侊紝鍙湁涓€涓垱鎰廝PT銆�
銆€銆€杩欎釜PPT锛屾簮浜庝竴涓ⅵ銆�
銆€銆€2010骞村啲鏃ョ殑涓€涓櫄锛屽惔闆ㄥ垵鍋氫簡涓€涓ⅵ銆傛ⅵ涓殑鐢佃剳灞忓箷涓婏紝鈥滅墻鐗涒€濅笌鈥滃崥鐗╅鈥濅袱涓瘝鍍忓姩鐢讳竴鏍锋嫾鍦ㄤ竴鍧楀効锛屽彉鎴愨€滅墻鐗涘崥鐗╅鈥濄€�
銆€銆€姝ゅ悗涓€涓湀锛屼粬鐔煡璧勬枡锛屽鍋歅PT锛屼竴鐐圭偣瀹屽杽鈥滅墻鐗涘崥鐗╅鈥濈殑鍒涙剰銆�
銆€銆€浠栫煡閬擄紝绾�3000骞村墠锛屾棌椹吇浜嗙墻鐗涳紝鍙堣鐗︾墰鍏昏偛锛氬悆鐗︾墰鑲夈€佸枬鐗︾墰濂躲€佺┛鐗︾墰鐨。鏈嶃€佷綇鐗︾墰姣涘笎绡枫€佺儳鐗︾墰绮仛楗彇鏆栤€︹€�
銆€銆€鏃犺浠庣敓瀛樿搴︼紝杩樻槸浠庢枃鍖栨剰涔変笂锛屾病鏈変换浣曚竴绉嶅姩鐗╀笌涓€涓皯鏃忕殑杩愶紝鍍忕墻鐗涗笌姘戞棌杩欐牱绱у瘑鐩稿叧銆傚彲闀挎湡浠ユ潵锛屽钀藉湪鑼尗楂樺師涓婄殑鐗︾墰鏂囩墿閬楀瓨锛屾病鏈夎繘琛岀郴缁熺殑鎼滈泦銆佹寲鎺樸€佺爺绌躲€佹暣鐞嗐€�
銆€銆€浜嗚В鍚撮洦鍒濈殑浜猴紝瀵逛粬鍋氳繖涓ⅵ锛屼竴鐐逛篃涓嶅鎬€傚洜涓洪珮鍘熶笂涓庣墻鐗涗负浼寸殑鏃忛樋濡堥樋鐖稿厔寮熷濡癸紝鏄粬鐨勯鑲変翰浜恒€�
銆€銆€绗竴娆℃彺16骞达紝浠庡亸杩滃熀灞傜殑涔℃枃涔﹁捣姝ワ紝鍚撮洦鍒濆湪楂樺師涓婂害杩囦簡鐐界儹鐨勯潚鏄ワ紝涔熼鏁欎簡椋庨洩銆佹壃娌欍€佷弗瀵掋€侀ゥ楗裤€侀珮鍘熷簲鍜屽锛屼絾鍚庢矇娣€鍦ㄨ蹇嗛噷鐨勶紝閮芥槸娴撳緱鍖栦笉寮€鐨勮皧銆�
銆€銆€鍚撮洦鍒濇案杩滆寰楋紝鏈夊勾鍐ぉ锛屼粬鍦ㄨ崏鍘熼獞琛岋紝琚瘨椋庡惞寰楁祽韬兊鍐凤紝璺岃惤鍦ㄤ竴椤跺笎绡疯竟銆傚笎绡烽噷涓€浣嶉樋濡堣劚涓嬩粬鐨勯澊瀛愶紝灏嗕粬鍐板喎鐨勫弻鑴氭彛杩涜瑗燂紝鐢ㄤ綋娓╀负鍚撮洦鍒濇殩鑴氾紝浠栨墠鍏嶄簬琚埅鑲€€傗€滄垜浠庢病浠庡摢鏈功閲岃鍒拌繃杩欐牱鐪熷疄鐨勫磭楂樸€傗€�
銆€銆€杩樻湁鐗︾墰銆�1977骞村啲锛屽惔闆ㄥ垵涓€琛岃鏆撮洩鍥板湪闆朵笅30鎽勬皬搴︾殑闃夸紛鎷夐洩灞憋紝楗ュ瘨浜よ揩涓拺浜�5澶�4銆傚槈榛庡幙濮斿緱鐭ユ秷鎭紝杩炲姩鍛樺悇瀹跺悇鎴风儥楗煎瓙閫佸幓鏁戞彺锛屾晳鎻磋溅寮€鍒颁腑閫旈櫡浣忥紝鎹㈡垚椹槦锛岄┈璧板埌闆繁澶勫張闄蜂綇锛屾崲浜嗙墻鐗涖€�
銆€銆€鈥滄垜浠嚑杩戠粷鏈涙椂锛岀湅鍒伴洩闄呭嚭鐜颁竴鐗囩偣锛岀煡閬撳幙閲屾晳鍒颁簡銆傝鍥扮殑浜轰滑鎹х潃楗煎瓙锛岀湅鐫€鍦ㄩ洩鍦板枠鐫€绮楁皵鐨勭墻鐗涳紝寰堝浜洪兘鍝簡銆傛槸鐗︾墰鏁戜簡鎴戜滑鐨勩€傗€�
銆€銆€澶氬勾鍚庯紝鍚撮洦鍒濆父璁茶捣杩欎釜鏁呬簨锛岃杩欏氨鏄粬鍒涘缓鐗︾墰鍗氱墿棣嗙殑璧峰洜銆�
銆€銆€鍜岃タ鐨勮皧鎵庝簡鏍癸紝鍥炰含宸ヤ綔鍚庯紝鏃犺澶氬繖锛屼粬浠庢湭涓庨珮鍘熶腑鏂仈绯汇€傚ソ鍑犱釜鏄ヨ妭锛屼粬璇锋棌鏈嬪弸鍒板寳浜竴璧疯繃銆�
銆€銆€2008骞达紝鍚撮洦鍒濆湪瑗垮伐浣滄椂鐨勮€侀儴涓嬫浠佹媺杈惧洜鍘讳笘銆傛浠佹媺杈剧殑濂冲効妗戞棪鎷夊崜锛屾垚浜嗗惔闆ㄥ垵鐨勬棌濂冲効銆佹枃鑰佸笀銆傗€滅埜鍟︼紙璇細鐖哥埜锛夊鎴戝儚瀵逛翰濂冲効涓€鏍凤紝浠栨槸鎴戠殑绗簩涓埗浜层€傗€�
銆€銆€鍚撮洦鍒濊锛氣€滄垜鐑埍瑗跨殑鍦熷湴鍜屼汉姘戯紝鎴戞€昏寰楄嚜宸变笉璇ユ槸楂樺師鐨勮繃瀹紝鎴戠殑鍚庡崐鐢熷簲璇ヤ細涓庤タ鑱旂郴鍦ㄤ竴璧枫€傗€�
鈥滃悜鐗︾墰瀛︿範鈥濓細涓哄缓鎴愬崥鐗╅锛屼粬鍍忕墻鐗涗竴鏍峰繝鍕囧敖
鍚撮洦鍒濆湪鎷夎惃绉熶綇鐨勫閲岋紝鏈夊箙鐢诲鏈嬪弸1988骞翠负浠栧垱浣滅殑鐢诲儚銆傜敾涓殑浠栬疆寤撳垰姣咃紝鍙岃€充笅闀垮嚭浜嗕竴瀵圭墰瑙掋€�
銆€銆€杩欏垎鏄庡凡缁忕偣鍑猴紝浠栬繖浜烘湁鐗涚殑鑴炬皵銆佺墰鐨勫潥姣咃紝骞跺皢涓庣墰缁撲笅涓嶈В涔嬬紭銆�
銆€銆€2011骞达紝鍚撮洦鍒濈敵璇疯緸鑱岃繑锛屽嚑浣嶅寳浜競棰嗗鍚簡浠栫殑鍗氱墿棣嗚鎯筹紝璁や负鍙互涓板瘜鍖椾含瀵瑰彛鎻村伐浣滅殑鍐呮兜銆傚競濮斿喅瀹氾紝灏嗙墻鐗涘崥鐗╅绾冲叆鎻村伐绋嬶紝杩欒鏈潵鎯斥€滃寲缂樼璧勨€濈殑鍚撮洦鍒濆垎澶栨儕鍠溿€�
銆€銆€鏃朵换鍥藉鏂囩墿灞€灞€闀跨殑鍗曢渷缈旓紝鍦ㄥ惔闆ㄥ垵绂讳含鍓嶅惉浜嗕粬鐨勮鎯筹紝璁や负瑕佽兘鍋氭垚锛岃繖灏嗘槸鈥滃浗鍐呭~琛ョ┖鐧姐€佷笘鐣屼竴鏃犱簩鈥濈殑鍗氱墿棣嗭紝琛ㄧず涓€涓湀鍐呬細鍘绘媺钀ㄧ湅浠栥€�
銆€銆€鈥滄垜涓€涓湀鍐呭绾﹀埌浜嗘媺钀紝鎴戝緢鏇夸粬鐫€鎬ワ紝浠栧綋鏃朵粈涔堥兘娌℃湁锛屼竴浠跺搧銆佷竴瀵稿缓绛戦兘娌℃湁锛屽彧鏈変袱涓棌闈掑勾褰撲复鏃跺織鎰胯€呫€傗€濆崟闇佺繑灏辫嚜鍛婂鍕囨垚浜嗙3鍙峰織鎰胯€呫€�
銆€銆€鍗曢渷缈旀湁鐞嗙敱涓哄惔闆ㄥ垵鐫€鎬ャ€傝櫧鐒跺崥鐗╅璧勯噾鏈変簡鐫€钀斤紝浣嗗叿浣撶殑寤鸿宸ヤ綔锛屾瘡鎺ㄨ繘涓€姝ラ兘澶毦銆�
銆€銆€3涓湀鍚庯紝鍦ㄥ寳浜競鍜屾媺钀ㄥ競棰嗗鐨勫叧娉ㄤ笅锛岀墻鐗涘崥鐗╅绛瑰鍔炲叕瀹ゆ寕鐗屾垚绔嬶紝鍖椾含甯傚張缁欏惔闆ㄥ垵鎸備簡鍖椾含鎻存寚鎸ラ儴鍓€绘寚鎸ュご琛旓紝鍗氱墿棣嗗缓璁惧ぇ澶ф彁閫熴€�
銆€銆€2012骞达紝鍚撮洦鍒濆紑濮嬪甫鐫€蹇楁効鑰呭鍏ㄥ浗鐗︾墰浜у尯鍋氱敯閲庯紝寰侀泦鏂囩墿锛屾€昏绋嬮暱杈�3涓囧叕閲屻€�
銆€銆€瀹濊吹鐨勬敹鑾凤紝鏄粬浠繖浜涜鍋氱墻鐗涘崥鐗╅鐨勪汉锛屽緱鍒颁簡鎳傜墻鐗涚殑鏃忓悓鑳炵殑鐞嗚В銆�
銆€銆€鏂囬噷娌℃湁鐜颁唬鎰忎箟涓婄殑鈥滃崥鐗╅鈥濇蹇碉紝鍚撮洦鍒濊窡浜鸿В閲婏紝浠栬寤虹殑鏄釜鈥滀簹棰囩珷鈥濓紝鍗斥€滅墻鐗涙鈥濄€傝繖璁╀粬杩呴€熻耽寰椾簡鐗ф皯浠殑蹇冦€�
銆€銆€鐢虫墡鍘跨殑鐗ф皯鏃ヨ鍚娑堟伅鍚庯紝涓€瀹跺叓鍙e繖娲诲嚑涓湀锛岀粐鎴愪竴椤剁墻鐗涙瘺甯愮锛岃鍎垮瓙鍧愪簡3澶╄溅閫佸線鎷夎惃銆傝繖鏄墻鐗涘崥鐗╅鑾锋崘鐨勪欢鍝併€�
銆€銆€姣斿鍘跨殑鎵嶅穿锛屽湪鍚撮洦鍒濅竴琛岀寮€鍚庯紝鎼滈泦鑷繁鍜屽叾浠栫墽姘戝閲屼笌鐗︾墰鏈夊叧鐨勭墿浠讹紝瑁呮弧鐨崱杞﹂€佸埌鎷夎惃锛岃繛閽变篃涓嶈偗鏀躲€�
銆€銆€鍒�2013骞达紝鍚撮洦鍒濆凡涓虹墻鐗涘崥鐗╅寰侀泦鍒�2000澶氫欢鍝侊紝鍏朵腑缇や紬鎹愯禒杈�40%浠ヤ笂锛屽湪鍥芥湁鍗氱墿棣嗕腑鍑犱箮缁濇棤浠呮湁銆�
銆€銆€2014骞�5鏈�18鏃ワ紝鍘嗙粡3骞磋壈杈涚寤猴紝瑗跨墻鐗涘崥鐗╅鍦ㄦ媺钀ㄥ紑棣嗭紝鍏辫鎰熸仼鐗︾墰銆佺墻鐗涖€佺浉浼寸墻鐗涖€佺伒缇庣墻鐗涘洓涓睍鍘咃紝寤虹瓚闈㈢Н8800澶氬钩鏂圭背銆�
銆€銆€鈥滄垜褰撲簡10骞村浗瀹舵枃鐗╁眬灞€闀匡紝瑙佽瘑杩囧緢澶氬崥鐗╅鐨勫缓璁撅紝浣嗘病鏈夊摢涓崥鐗╅鐨勭寤鸿繃绋嬪姝ゆ劅浜恒€傗€濇椂浠绘晠鍗氱墿闄㈤櫌闀垮崟闇佺繑鍦ㄧ墻鐗涘崥鐗╅寮€棣嗕华寮忎笂璇淬€�
銆€銆€鈥滄垜鐭ラ亾杩欎釜杩囩▼涓粬鏈夊涔堣壈闅撅紝鍋氫簡澶氬皯宸ヤ綔銆傛槸浠栧鍗氱墿棣嗙殑鐞嗚В銆佸瑗挎枃鍖栫殑鐞嗚В銆佸瑗块偅鐗囧湡鍦扮殑鐑埍锛屼娇浠栧仛鎴愪簡涓€鐣簨涓氥€傗€濆崟闇佺繑鍏呮弧娣卞湴鍥炲繂銆�
鈥滄棤瑷€鐨勬垬鍙嬧€濓細鍚撮洦鍒濆彂鐜扮墻鐗涙枃鍖栦篃鏄孩鐨�
2019骞�7鏈�1鏃ワ紝鍚嶄负銆婃棤瑷€鐨勬垬鍙嬨€嬬殑灞曞湪瑗跨墻鐗涘崥鐗╅寮€骞曘€傝繖鏄粰涓浗寤�98鍛ㄥ勾銆佷腑鍗庝汉姘戝叡鍜屽浗鎴愮珛70鍛ㄥ勾銆佸窛鍜岄潚鍏矾閫氳溅65鍛ㄥ勾銆佽タ姘戜富鏀归潻60鍛ㄥ勾鐨勭尞绀笺€�
銆€銆€鈥滄棤瑷€鐨勬垬鍙嬧€濆氨鏄墻鐗涳紝杩欐槸鍚撮洦鍒濈殑鍙戠幇銆�
銆€銆€2018骞村澶╋紝鍚撮洦鍒濆湪鎴愰兘琛楀贩娣卞鍑犵粡杈楄浆锛屽湪骞蹭紤鎵€鎵惧埌浜�98宀佺殑瑙f斁鍗佸叓鑰佸悓蹇楅瓘鍏嬨€傝繖鏄笌瑗跨粨缂樼殑涓や唬鍐呭湴骞查儴鐨勪竴鍦衡€滅墻鐗涗細鈥濄€傛鍓嶏紝鍚撮洦鍒濆湪鐮旂┒鐗︾墰瀵逛腑鍥介潻鐨勮础鐚椂鍙戠幇锛屽綋骞翠翰鍘嗗崄鍏繘銆佸拰骞宠В鏀捐タ鐨勯瓘鍏嬶紝鏇剧敤鈥滄棤瑷€鐨勬垬鍙嬧€濆舰瀹圭墻鐗涖€�
銆€銆€鎹瓘鍏嬩簡瑙o紝鍦ㄥ窛銆侀潚鍏矾閫氳溅鍓嶇殑杩�5骞存椂闂撮噷锛屾棌浜烘皯鍑哄姩鐗︾墰100澶氫竾澶存敮鎻磋В鏀捐繍杈撱€傝繖浜涚墻鐗涳紝涓嶄粎缁欓儴闃熻繍鏉ヤ簡鐗╄祫锛岃€屼笖杩樻槸瑙f斁鍦ㄥ啺澶╅洩鍦拌繘鏃剁殑寮€璺厛閿嬨€�
銆€銆€鍚撮洦鍒濇洿澶氱殑鐮旂┒鍙戠幇锛屼护鎴戜滑瀵光€滄棤瑷€鐨勬垬鍙嬧€濇洿鍔犺們鐒惰捣鏁細
銆€銆€鈥斺€旂孩闀垮緛杩囬洩灞辫崏鍦帮紝鏃忎汉姘戣刀鐫€鐗︾墰鏀彺绾€€傞潻鑳滃埄鍚庯紝姣涙辰涓滄浘瀵规棌鑰佺孩澶╁疂璇达細鈥滀腑鍥介潻鍦ㄦ煇绉嶆剰涔変笂璇村氨鏄€樼墻鐗涢潻鈥欍€傗€�
銆€銆€鈥斺€旇В鏀惧崄鍏€佸悓蹇楃帇璐佃锛氣€滆タ鍜屽钩瑙f斁鐨勮儨鍒╋紝鏄殑鏀跨瓥鐨勮儨鍒╋紝涔熸槸鏃忎汉姘戠敤鐗︾墰椹嚭鏉ョ殑銆傗€�
銆€銆€鈥斺€�1950骞达紝浜烘皯瑙f斁杩涜タ銆傚綋鏃舵病鏈夊叕璺紝閮ㄩ槦缁欏吇鍏ㄩ儴闈犱汉鑳岀墰椹€傛棌鏀墠妯¤寖鏇茬編宸寸弽璧剁潃鑷鐗︾墰涓轰汉姘戣В鏀鹃┊杩愮墿璧勶紝鑷充粖浠嶈棰傘€�
銆€銆€鈥斺€斾笂涓栫邯80骞翠唬锛岄樋閲屾尝鏋楄竟闃茶繛鎴樺+鏀跺吇浜嗕竴澶存棤浜鸿棰嗙殑鐗︾墰锛屽畠涓烘垬澹┊姘�10澶氬勾锛岀洿鑷宠“鑰併€傛垬澹滑鏇句负瀹冨缓澧撶珛纰戯紝杩樺悜鍗楃枂鍖虹敵鎶ュ苟鑾峰噯涓哄叾璁颁笁绛夊姛锛岃繖鍦ㄥ叏鍘嗗彶涓婁竴鏃犱簩銆�
銆€銆€鐗︾墰鏂囧寲涔熸槸绾㈢殑銆傚湪鎷夎惃甯傗€滀笉蹇樺垵蹇冦€佺墷璁颁娇鈥濅富棰樻暀鑲叉湡闂达紝寰堝鍗曚綅缁勭粐鍛樺共閮ㄥ弬瑙傘€婃棤瑷€鐨勬垬鍙嬨€嬪睍銆傚湪杩欓噷锛屼粬浠兘鍚埌鍗氱墿棣嗛噷銆婂垵蹇兟蜂娇銆嬬殑绔ュ0鍚堝敱鈥斺€�
銆€銆€鈥滄垜浠笉蹇樺垵蹇冿紝浜旀槦绾㈡棗椋樻壃鍠滈┈鎷夐泤锛涙垜浠墷璁颁娇锛岃タ澶у湴寮€閬嶅垢绂忎箣鑺便€傚晩锛屽瞾鏈堟祦娣岋紝杩芥ⅵ鑰呮案鍚戝ぉ娑€傗€�
銆€銆€杩欐瓕锛屼綔璇嶇殑鏄惔闆ㄥ垵銆�
銆€銆€杩芥ⅵ鑰呮案鍚戝ぉ娑€傝繖鏄潻鍓嶈緢鐨勭簿涓嶆溄銆�
銆€銆€杩芥ⅵ鑰呮案鍚戦珮鍘熴€傝繖鏄憳鍚撮洦鍒濈殑鍒濆績娴佹穼鈥斺€斾粬鐨勫績锛屾案椹荤簿楂樺湴銆�
鈥滆繖杈堝瓙澶熶簡鈥濓細鏂囧寲鎻达紝鍖椾含鐨勨€滃惔闆ㄥ垵鈥濆彉鎴愯タ鐨勨€滀簹鏍煎崥鈥�
鍚撮洦鍒濆緢鍠滄鑷繁鐨勬枃鍚嶅瓧锛屽彯鍢辫鑰呪€滃氨鍙垜浜氭牸鍗氣€濄€備粬鎶婅嚜宸辩殑浜虹敓浠峰€间笌寮樻壃鐗︾墰鏂囧寲绱х揣鎷村湪涓€璧枫€�
銆€銆€璁拌€呴噰璁挎椂锛屼竴瀹跺叕鐩婃満鏋勫皢涓€缇ゆ潵鑷寳楂樻捣鎷旂墽鍖哄弻婀栥€侀潰棰婄孩鐨勫皬涓€璺甫鑷冲寳浜父瑙堬紝鐗︾墰鍗氱墿棣嗘槸浠栦滑鍒版媺钀ㄥ悗鐨勭涓€绔欍€�
銆€銆€娲诲姩缁勭粐鑰呰寖涓借锛氣€滆繖浜涘瀛愰兘鏄涓€娆¤蛋鍑哄寳鐗у尯锛岀涓€娆″埌鎷夎惃锛屼粬浠鏈皯鏃忓巻鍙叉枃鍖栫殑浜嗚В鍑犱箮鏄浂锛岀墻鐗涘崥鐗╅鎭版伆鍙互濉ˉ杩欎釜绌虹櫧銆傗€�
銆€銆€鍚撮洦鍒濆枩娆㈠湪鐗︾墰鍗氱墿棣嗛噷鐪嬪埌瀛╁瓙锛屼粬浠庝腑鎰熷彈鐫€涓€涓皯鏃忓巻鍙叉枃鍖栫殑鎵裤€�
銆€銆€鍦ㄥ惔闆ㄥ垵鐪嬫潵锛岀墻鐗涙枃鍖栨槸涔呰繙鍜屽箍娉涚殑瑗挎皯鏃忔皯闂存枃鍖栦箣涓€锛屽缓绔嬬墻鐗涘崥鐗╅鑳介€氳繃鐗︾墰杩欎竴杞戒綋锛屽憟鐜板叾鎵€椹浇鐨勮タ鍘嗗彶鍜屾枃鍖栵紝缁堝舰鎴愮殑瑗挎枃鍖栫鍙枫€�
銆€銆€鐗︾墰鍗氱墿棣嗕功璁扮惣鐝嶅憡璇夎鑰咃紝寮€棣�5骞达紝鍙傝鑰呯疮璁℃暟鍗佷竾浜烘锛岃繖閲屾垚涓轰汉浠簡瑙hタ鐨勭獥鍙c€�
銆€銆€鍚撮洦鍒濊锛氣€滅墻鐗涗綔涓洪珮鍘熶箣瀹濓紝鍑犲崈骞存潵涓庨珮鍘熶汉姘戠浉浼寸浉闅忥紝鎴愬氨浜嗘棌浜烘皯鐨勮。銆侀銆佷綇銆佽銆佽繍銆佺儳銆佽€曪紝娑夊強楂樺師鐨勬斂銆佹暀銆佸晢銆佹垬銆佸ū銆併€佹枃锛屽苟娣卞埢褰卞搷浜嗛珮鍘熶汉姘戠殑绮炬牸锛屾壙杞界潃楂樺師浜烘皯鐨勫杽鑹笌鍕ゅ姵銆佸潥闊т笌鍘氶噸锛屾槸闈掗珮鍘熶竴涓殑璞″緛鍜岀鍙枫€傗€�
銆€銆€涓烘锛屼粬甯屾湜鍏朵粬姘戞棌鐨勪汉浠兘鍥犱负鐗︾墰鍗氱墿棣嗘洿鐞嗚В瑗垮拰鏃忋€傛瘡娆″唴鍦板贰灞曪紝浠栦滑閮戒細鏀跺埌寰堝棣堛€傛湁鍦ㄦ媺钀ㄥ綋杩囩殑瑙備紬鎵ф剰鎶婄弽澶氬勾鐨勮€佹崘缁欑墻鐗涘崥鐗╅锛涙湁鎻磋繃鐨勮€佷汉璇磋嚜宸辨槸鐜板満楂樺叴鐨勪汉锛屽洜涓哄張瑙佸埌浜嗙墻鐗涳紱鏈夋病鍘昏繃瑗跨殑瑙備紬锛岃鍦ㄥ睍瑙堜笂浣撲細鍒拌タ鐨勬枃鍖栵紱鏈夊勾杞讳汉璇寸湅鍒颁簡涓嶄竴鏍风殑瑗库€︹€︽洿澶氫汉璇达紝鎴戜竴瀹氳鍘昏タ鐪嬬湅銆備汉浠锛屽惔闆ㄥ垵鏄粰瑗挎梾娓稿仛骞垮憡鍛€€�
銆€銆€浠婂勾锛屽惔闆ㄥ垵宸茬粡65宀侊紝瑙夊緱璇ョ粰鐗︾墰鍗氱墿棣嗘壘浣嶆柊棣嗛暱浜嗐€傚彧鏄紝瑕佹壘涓€涓兘鍦ㄥ悇灞傞潰鎺ユ浛浠栫殑鏂伴闀垮疄闈炴槗浜嬨€�
銆€銆€鏈夋椂鍊欙紝鍚撮洦鍒濅細鎬濊€冧竴涓汉鐨勪环鍊煎埌搴曚綍鍦ㄣ€備粬瑙夊緱鑲畾涓嶅湪浜庤兘鎸e灏戦挶銆佹湁澶氬ぇ鍚嶏細鈥滄垜杩欎釜浜哄暐涔熶笉浼氾紝鍋氫簡鐗︾墰鍗氱墿棣嗭紝杩欒緢瀛愬浜嗐€傗€�
銆€銆€鍦ㄦ媺钀紝鎴戜滑鏇惧悜璁稿浜哄惉鍚撮洦鍒濇槸涓€庢牱鐨勪汉锛屽緱鍒扮殑鍥炵瓟鏄彟涓€浜涢棶棰橈紝姣斿锛氣€滆繖涓勾浠o紝鎬庝箞杩樻湁杩欐牱鐨勪汉锛屾斁寮冨湪鍖椾含鐨勭敓娲伙紝鎷间负鏃忓拰鐗︾墰鍋氫竴浠朵簨锛熲€�
銆€銆€鈥滄皯鏃忓洟缁撻潬鐨勫氨鏄繖鏍风殑浜嬶紝杩欐牱鐨勪汉銆傗€濅粬鐨勬棌鏈嬪弸浠洖绛斻€�